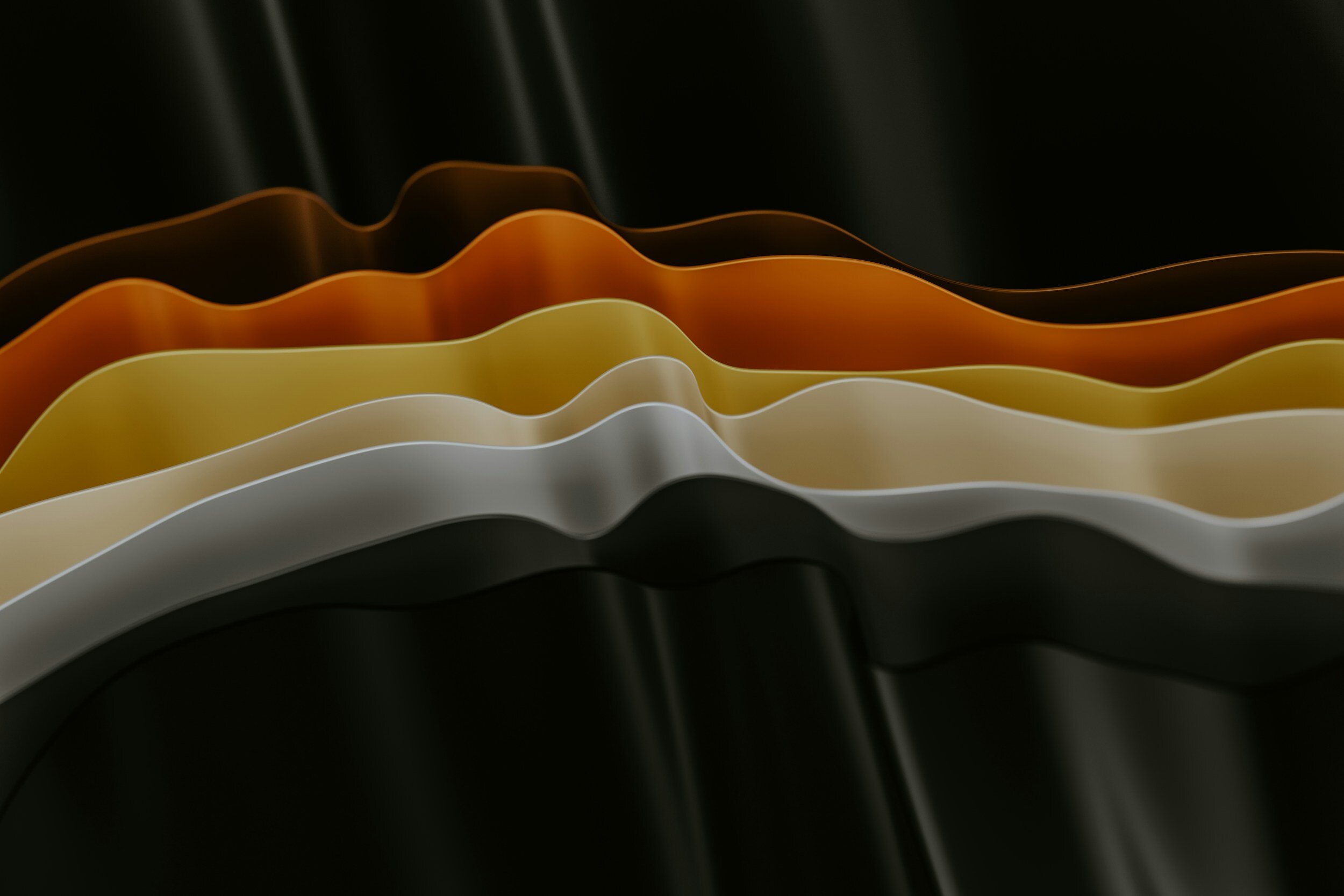
ABOUT HBC
Owner, Peter Huerst
For more than 20 years, I was a leader and executive in the Automotive industry, holding various positions in Operations and Supply Chain Management, from entry level to Director. I worked with cross-functional teams and external partners to ensure alignment, coordination, and collaboration.
Being fluent in English and German has always been a plus in working with international teams on both sides of the pond. Understanding the multi-cultural differences and nuances has greatly helped me to support diverse working environments.
I provided leadership, strategy and vision, inspiration, and motivation to my staff. I have developed and honed my skills in operational excellence, process improvement, stakeholder management, and data-driven decision making, and have launched cost-saving, quality-enhancing, and risk-reducing initiatives.
My goal has always been to meet and exceed the expectations of those I have worked with while optimizing processes in pursuit of operational excellence.
I enjoy working in a dynamic and collaborative environment. I like creating value for customers and contributing to their success through the application of my knowledge and skills. It is important to me to listen to my customers carefully, understand their needs, and to work with them and develop solutions with and for them and help them in the execution of their plan.
PERSONAL BACKGROUND AND INTERESTS
I built my professional foundation on an Engineering degree I obtained at the University of Applied Sciences in Karlsruhe, Germany, in German “Diplom Wirtschaftsingenieur”.
I arrived in the Lehigh Valley in 2001 from my German home-state of Baden-Wuerttemberg, which lies in the Southwest bordering France and Switzerland. The Baden region is home to the world-famous Heidelberg Castle. After relocating to the USA, I found my permanent home in Heidelberg Township in Pennsylvania. A German to live in Germansville, with close connections to Heidelberg and Baden, that is where everything ties together.
I enjoy travelling with my wife, spending quality time with my two kids, and keeping up with two grandsons.
I am a self-taught fine arts painter, avid model railroader (H0) and like to keep “Gunther” alive (My sourdough starter – if you know you know.)
VALUE PROPOSITION
Our team is flexible, fast, can provide expert advice and can work on short deadlines. We support data-driven decision making and seek cost-saving, quality-enhancing, and risk-reducing initiatives.
As a virtual company without overhead costs or strict corporate rules, we save our clients time and money, and establish a flexible workplace for getting things done.
We like to capitalize on opportunities that are geographically close as we start and grow our business.
Our strength is the comfort with financial data and our systematic and analytical ability.
Working with clients, we are unassuming in our questioning, pragmatic in our approach and attentive to our client’s needs.
REFERENCE PROJECTS
2002
I was project leader for an implementation of ERP Systems, moving from SAP R/2 to R/3. At the same time, I managed the relocation of a warehouse operation from Virginia to Pennsylvania.
2005
By 2005, the warehouse with 60,000 Square feet was insufficient in size, and subsequently, I led a team to relocate it and integrate into a 125,000 square feet location within the business park.
As part of this project, two administrative office locations were consolidated and relocated to the new warehouse site.
2012
To improve the warehouse operation, I launched a Warehouse management system upgrade within SAP R/3, tailored to our Automotive distribution process and Aftermarket customer requirements.
2016
I was the project lead to open a 78,000 square satellite warehouse facility in order to improve the performance and reduce bottlenecks; at the same time, we configured a new SAP Warehouse Management module for the operation.
2021
During the COVID Pandemic, I was responsible for ramping down the operation to follow state regulations, but then reopening the facility as essential business, following all of the corporate and state guidelines to operate during a Pandemic. I had two weeks to get the organization ready and the facilities prepared to function again.
2022/2023
I was project leader for the launch of a 3PL Warehouse in Texas with 168,000 square feet. I was responsible for the installation of the IT infrastructure and network, and also for the concurrent launch of a SAP Warehouse management system for the new site.